Pentingnya pengujian pada sistem perpipaan terletak pada perlunya memastikan bahwa pipa, sambungan, dan komponen lainnya beroperasi secara efisien dan aman. Kegagalan pada sistem perpipaan dapat mengakibatkan kebocoran, kerusakan lingkungan, bahkan kecelakaan fatal. Dua pendekatan yang umum digunakan dalam pengujian sistem perpipaan adalah destructive test dan non-destructive test.
Dalam artikel ini, kita akan membahas kedua metode pengujian tersebut, serta peran dan implikasinya dalam menjaga keamanan dan keandalan sistem perpipaan.
Destructive dan Non-Destructive Test dalam Sistem Perpipaan
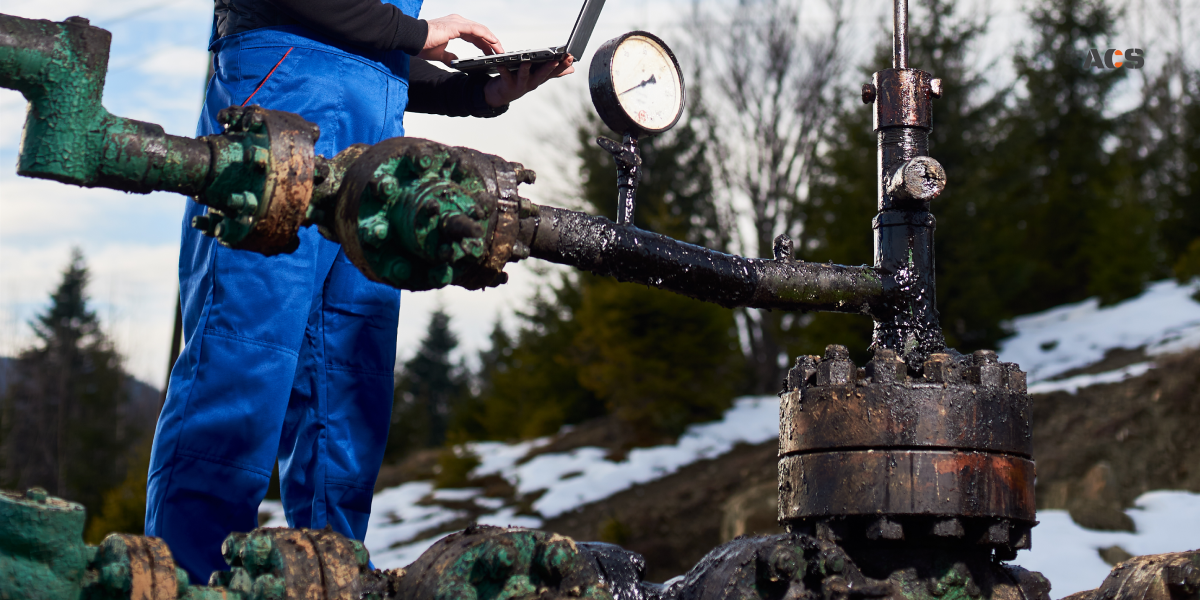
Implementasi destructive dan non-destructive test pada sistem perpipaan biasanya dilakukan dalam tahap pengembangan material baru, pemilihan material untuk proyek konstruksi, atau pemantauan kualitas dalam penggunaan sistem perpipaan yang sudah ada.
Destructive Test
Destructive test, atau uji penghancuran, merupakan salah satu metode penting dalam menguji integritas struktural pada komponen atau material tertentu. Dalam konteks sistem perpipaan, destructive test bertujuan untuk mengevaluasi tingkat kekuatan, kekerasan, dan keausan material pipa.
Meskipun penggunaan metode ini dapat merusak sampel yang diuji, namun hasilnya memberikan informasi dalam memahami karakteristik dan memastikan kualitas sistem perpipaan secara keseluruhan.
Baca Juga: Teknik-teknik dalam Inspeksi Pipa
Metode yang Dilakukan dalam Destructive Test
Metode ini mencakup berbagai teknik pengujian, di antaranya adalah tensile test, compressive test, bending test, dan hardness test. Berikut penjabarannya:
Hardness Test (Uji Kekerasan)
Hardness test dapat menentukan tingkat kekerasan suatu material, yang berkaitan erat dengan ketahanan material terhadap penetrasi, keausan, atau deformasi. Serta kemampuan material atau komponen dalam menahan abrasi yang mungkin terjadi selama penggunaan.
Bending Test (Uji Lentur)
Bending test bertujuan untuk mengevaluasi kekuatan lentur atau fleksibilitas dan menilai kemampuan komponen untuk menahan beban lateral atau gaya lentur. Pengujian ini dilakukan dengan pemberian beban lateral pada sampel pipa hingga terjadi patahan. Hasil dari bending test memberikan informasi tentang kekuatan lentur serta titik-titik kritis di mana komponen rentan terhadap kerusakan.
Compressive Test (Uji Tekan)
Compressive test berperan mengukur kekuatan tekan. Dalam konteks sistem perpipaan, compressive test membantu dalam mengevaluasi kemampuan komponen untuk menahan tekanan eksternal. Prosedur pengujiannya melibatkan pemberian beban tekan pada sampel pipa hingga terjadi deformasi atau patah. Hasil dari compressive test memberikan informasi tentang tegangan maksimum yang dapat ditahan oleh material pada kondisi tekanan.
Tensile Test (Uji Tarik)
Metode ini dilakukan untuk mengukur kekuatan yang melibatkan pemberian beban tarik secara gradual pada sampel pipa hingga terjadi patah atau retakan. Dari hasil tes ini, dapat diperoleh data tentang tegangan maksimum yang dapat ditahan oleh material (ultimate tensile strength) dan titik leleh (yield point), yang merupakan parameter penting dalam mengevaluasi kekuatan material pipa.
Non-Destructive Test
Non-Destructive Test (NDT) adalah metode pengujian yang digunakan untuk memeriksa integritas material, komponen, atau struktur tanpa merusak atau mengubah sifat-sifat material secara permanen. Tujuan utama dari NDT adalah untuk mendeteksi cacat atau ketidaksempurnaan pada material atau komponen tanpa mengganggu operasional atau fungsionalitasnya.
Metode yang Dilakukan pada Non-Destructive Test
Metode ini mencakup berbagai teknik pengujian, di antaranya adalah radiografi, ultrasonik, eddy current testing, dan magnetic particle testing. Berikut penjabarannya:
Radiografi
Radiografi yang dimaksud menggunakan sinar-X atau sinar gamma untuk menembus material dan menghasilkan gambar tentang struktur internal dan kualitas komponen. Dengan radiografi, cacat seperti retakan, inklusi, atau korosi dapat dideteksi dengan memperhatikan perbedaan dalam kepadatan material yang direkam dalam gambar radiografi.
Ultrasonik
Metode ultrasonik menggunakan gelombang ultrasonik yang dikirimkan ke dalam. Gelombang ini akan dipantulkan kembali dari permukaan atau dari bagian dalam material, dan perubahan dalam gelombang ini digunakan untuk mengevaluasi keberadaan cacat atau ketidaksempurnaan dalam material, seperti retakan atau perubahan struktur.
Eddy Current Testing
Eddy current testing melibatkan penggunaan medan elektromagnetik yang dihasilkan oleh arus listrik yang melewati probe khusus. Perubahan dalam medan elektromagnetik yang dihasilkan oleh Eddy Current pada material digunakan untuk mendeteksi cacat atau ketidaksempurnaan, seperti retakan atau perubahan konduktivitas material.
Magnetic Particle Testing
Metode ini menggunakan partikel-partikel magnetik yang diterapkan pada permukaan material yang akan diuji. Ketika medan magnet diterapkan, partikel-partikel ini akan menumpuk di sekitar cacat atau retakan, membentuk pola yang dapat diamati oleh operator pengujian, memberikan indikasi tentang lokasi dan ukuran cacat tersebut.
Membandingkan Destructive dan Non-Destructive Test
Destructive test dan non-destructive test menggambarkan ada banyak pendekatan berbeda dalam menguji integritas komponen perpipaan. Destructive test, seperti yang sudah dijelaskan, secara aktif berpotensi merusak sampel material dengan tujuan untuk memahami sifat-sifat mekanisnya. Di sisi lain, non-destructive test, mempermudah inspeksi material tanpa mengubah atau merusak sampel secara permanen, memberikan gambaran tentang kondisi internal dan permukaan material.
Meskipun destructive test memberikan pemahaman yang mendalam tentang sifat-sifat material, namun prosesnya membatasi penggunaan kembali sampel uji dan memerlukan biaya serta waktu yang lebih besar. Sementara itu, non-destructive test lebih cepat dan efisien, namun memiliki keterbatasan dalam mendeteksi cacat yang tersembunyi atau dalam memahami sifat-sifat material secara mendalam.
Dalam pengujian sistem perpipaan, pemilihan antara destructive test dan non-destructive test harus dipertimbangkan dengan cermat berdasarkan kebutuhan spesifik pengujian dan kondisi sistem perpipaan yang ada. Pemilihan satu di antara dua tes tersebut diharapkan dapat tetap membantu kinerja sistem, tanpa menimbulkan potensi kerugian setelah pengujian dilakukan.